生产效率是以工作时间来衡量的,企业做好时间分析,找出不合理的时间并及时改善,就能提升生产效率。
所以,作为一名优秀的管理者,就需要随时随地关注员工作业时间,分析其合理性——是否有理分配?是否存在浪费?是否创造价值?把每日的时间进行统计分析,就很容易发现管理的问题所在。
除了直接作业时间外,我们还是需要一些准备时间、异常时间、切换时间、生理时间、款放时间等。而这些时间都不会产生任何价值,这就是我们改善管理的关键。
理论上,100%的时间产出100%的价值是每一个卓越管理者所追求的,但实际上我们很难达到这个状态。
在多年的经验里,我们常能遇到生产管理者提及产能不足的问题,思博老师测定并发现其有效时间的利用率在50%~70%的区间波动,这意味着企业其实有30%~50%的时间未被有效利用。
管理者能够发现改善空间,就意味着企业已经在改善的路上。
本期采用公司辅导的 “精益生产管理” 相关案例来做剖析,了解思博老师 如何通过时间管理、产能提升、工艺改善等方式帮助企业提升综合效能。
G企业是专注于三相异步电动机、电动车电机、摩托车发动机、摩托车发动机配件等制造及房地产开发等多元化产业、经济技术实力雄厚的大型集团化企业。公司一直致力于研发技术团队搭建与培育、品质保证能力提升,及生产技术设备改良与转型升级,依靠高质量和个性化设计赢得了越来越多客户的认可。
G企业面临人员招聘困局,而订单却源源不断,需求大于供给过半,企业的当前产能无法满足市场需求。
生产管理焦头烂额、手足无措——公司提供的人、机、料等生产要素不足;销售消极疲累、抱怨四起——客户因订单交付的延期感到不满,影响后续合作......
外部环境
年底订单量突增,实际生产能力超荷;
年关将至,缺人且人员招聘无进展;
企业面临难得的发展机遇。
内部管理
抱怨缺人、设备旧等,未认清管理问题;
有意愿提升产能,缺少方式方法;
产能提升仅靠外协与加班解决;
部门之间相互指责与抱怨。
G企业虽有制定各产品及工序标准工时与节拍,但一直未进行设备稼动率统计及原因分析;同时,通过对人均小时产值的数据分析,发现员工时间利用率不高,无形中浪费了产能。
因前期缺少数据统计与分析,项目组老师对冲铸车间数据进行统计发现:设备稼动率(时间稼动率×性能稼动率)仅67.04%;内部资源利用率不足,是产能提升受阻的重要原因。
车间现场
❶ | 重铸车间现场废料零散,员工每天需要半小时以上的时间清理现场,影响员工价值贡献,无价值时间过多; |
❷ | 上班时间员工尚未进入工作状态,现象普遍,每天5分钟,影响1.04%的产出; |
❸ | 重铸换料日均三次,每次15分钟,料完才换,影响 9.3%的产量; |
❹ | 上班后设备停止,开机时间长,造成等待浪费; |
❺ | 产品大量返工返修,车间主管对无价值工作的多少一无所知; |
❻ | 铸件设备停机,无人换取料件,无效加工15分钟,生产效率减少3.125%; |
❼ | 未对设备进行定期保养,因设备调整,早上常常出现集体 “罢工” 的现象; |
❽ | 员工提前离开工作岗位3分钟,影响0.6%的效率; |
❾ | 节拍不稳定,影响性能稼动率; |
❿ | 设备性能落后,速度影响10%的效率。 |
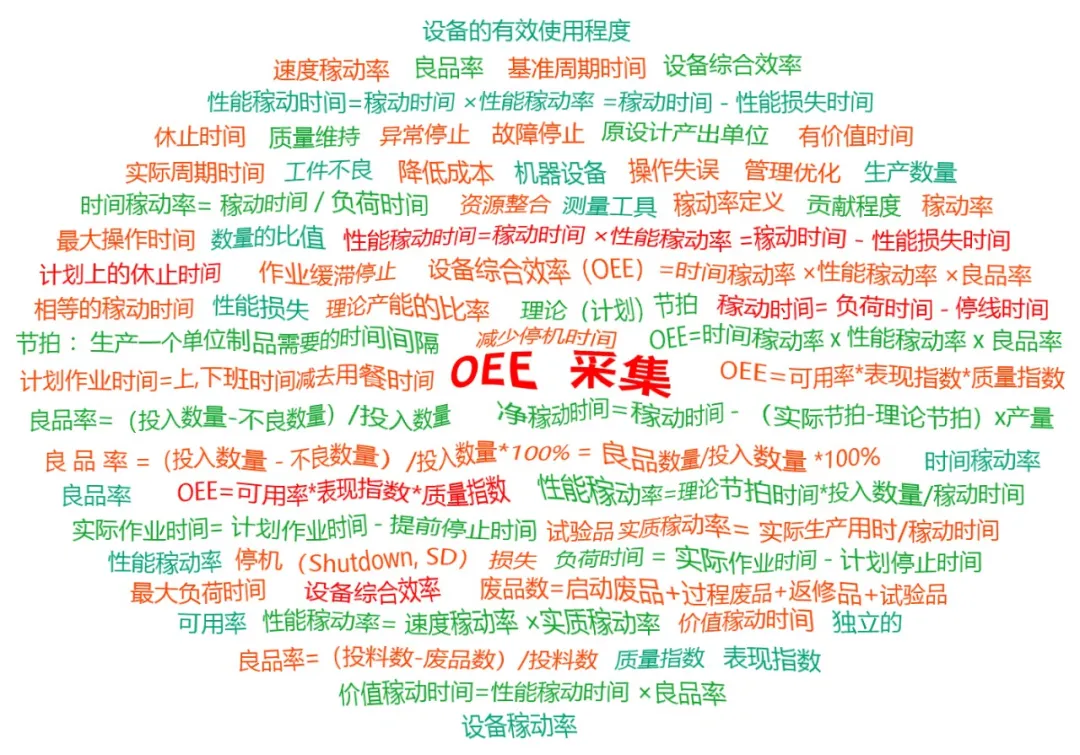
稼动率是指设备在所能提供的时间内为了创造价值而占用的时间所占的比重,即一台机器设备实际的生产数量与可能的生产数量的比值。
而稼动时间是指负荷时间减掉换模、换刀具、故障、调整等的时间。因此要提高稼动率,就必须要减少换模具、换刀具、故障、调整的损失时间。如果能将这些损失时间减为零,那么稼动率就可以达到百分之百。
因而,对员工的产值提升培训、时间管理的增强与工艺的改善,是本次项目解决的重点。
采集了现场现象与部分数据,针对现场问题,梳理管理思维,辅导管理技能技巧。
培训中,我们展现了现场时间分析成果,学习与案例相结合,融汇贯通管理知识;同时,让管理认识到实际存在的问题,并培训解决方案与技巧。
培训后,为了深入管理,让大家更加明白其他改善措施,提升设备稼动率及产能的利用率,采取了减少前置时间、动作浪费和改善工装等措施;并在生产现场、办公室现场进行一对一辅导、研讨等,进一步巩固时间分析培训的成果。
除了时间分析,培训还涉及了产能管理、物控管理、稼动率分析。
经过三周的驻厂辅导后,设备稼动率得到明显改善,产值也在年底创了一个新高。
产能与效率也有显著的提升,改善效果远超培训时预想的5.2%——总共提升了24%的产能。
车间稼动率从当初在50%~70%的区间波动,到改善后基本稳定,并且不低于85%。
人员与资源的配置同步优化,车间人数减少9.91%,加班时间仅提升7.03%,人均产值提升26.27%。
结语
设备存在六大损失,包括故障、调整、空转、速度、不良、启动。要提高设备的综合效率,就必须从源头上消除这六个损失。
此外,人的因素是第一位的,解决了人的问题才能解决设备的问题。
经营管理,成本分析
要追根究底、分析到最后一点