在制造业中,对产品品质有直接影响的通常为设计、来料、制程、储运四大主项,一般来说设计占25%,来料占50%,制程占20%,储运1%~5%。综上所述,来料检验对公司产品质量占压倒性的地位,所以要把来料品质控制升到一个战略性地位来对待。
品质管理的核心是质量,基础是全面参与,宗旨是让客户满意,最终目的是形成一套长期成功的管理途径。总结起来,品质管理一般包含三个方面,即来料品质管理、制程品质管理、出货品质管理,企业可从以上三方面突破品质管理,寻找最优方法。
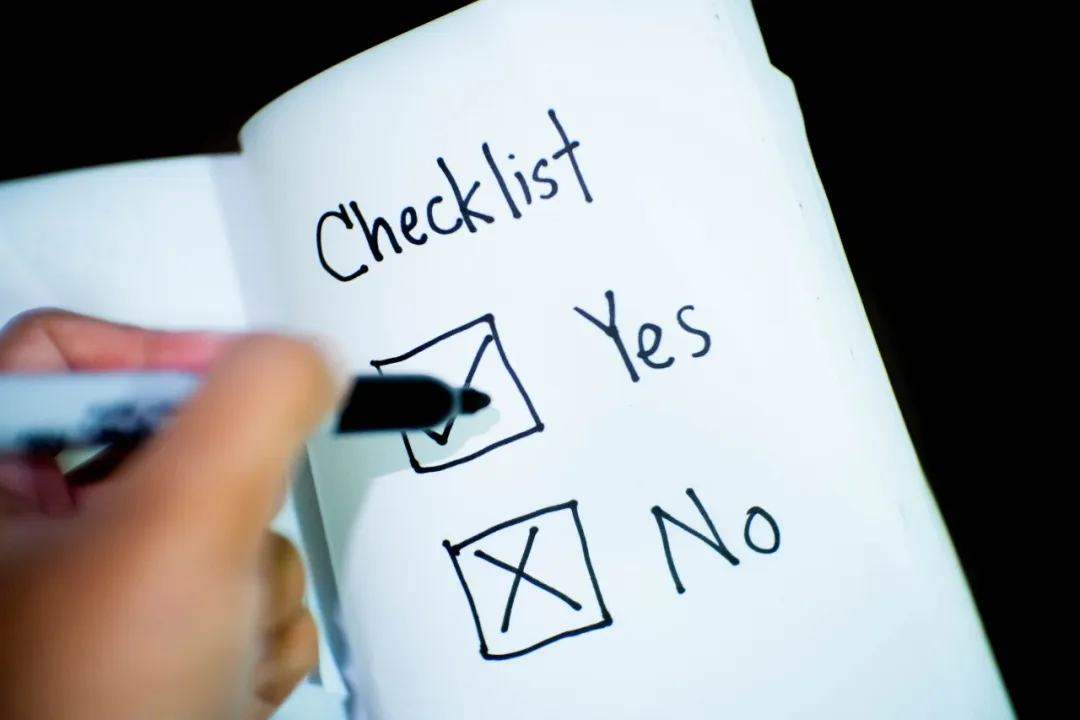
本期采用公司辅导的 “品质管理” 相关案例来做剖析,了解思博老师 如何帮助企业提高来料合格率、减少生产异常与不良现象。
A企业专主要经营范围为音响产品的研发、生产和销售,音箱的生产和销售,电子、五金、塑胶产品的生产和销售。公司运用ISO9001质量管理体系,实施严格的质量管理,确保产品品质。 公司所有系列音响产品均为自主研发,同时保持与国名知名院校的科技合作,以占领技术领域的国内领先水平;公司产品有蓝牙、WIFI/智能影院、汽车音响等。A企业积极推广自主品牌、开拓国内市场,同时将继续保持与国内外著名品牌如HP、联想、创新科技、飞利浦等客户的合作,全部工程竣工后,达到年产500万套产品,年营业额数亿元以上。
在初步的沟通与数据统计中, 我们了解到:
公司销售业绩年增幅为52%,月增幅为31%,单从业绩的增长来看企业的发展还是比较良性的;
抓取某年最高人均产值与最低人均产值作比较,差距较大,最高人均产值比最低值高出120%,生产效率波动大;
某年1~11月,公司直接制造成本平均占售价比90.86%,严重超出同行业平均水平;
根据某年制程异常反馈单,1~11月所产生的异常工时数是8687个小时,其中因供应商来料异常占比近19%,供应商管理体系没有发挥应有的作用。
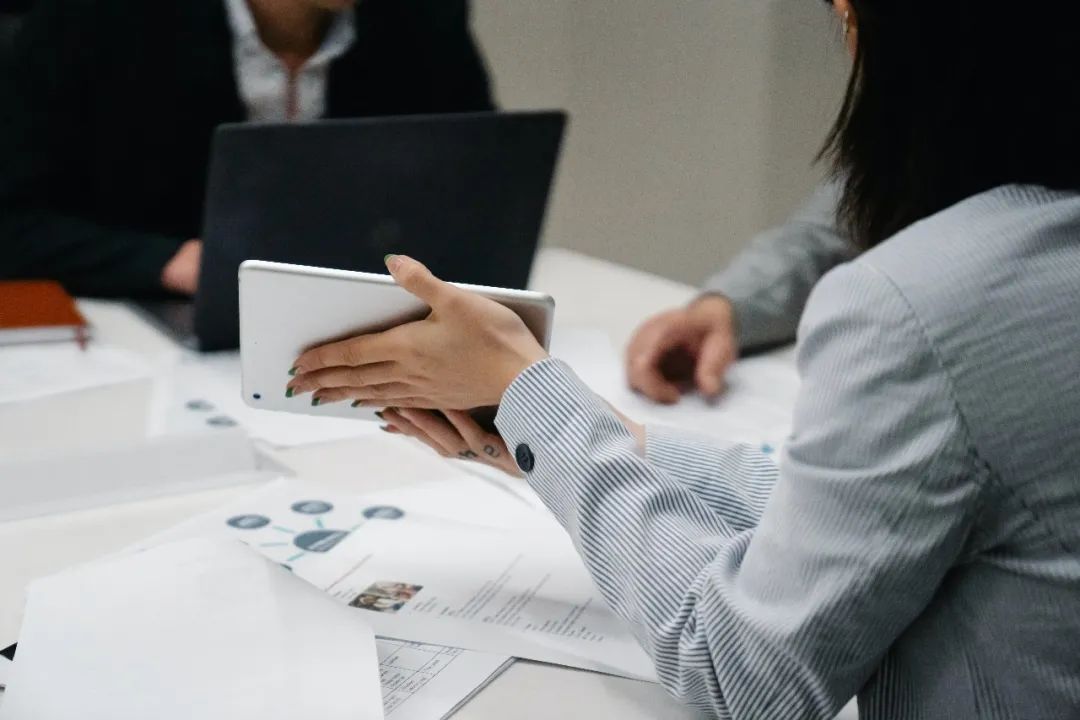
针对来料的品质问题,我们对各个月份的来料不良异常工时进行排查,并统计各月来料批次送检合格率:异常工时持续增长,来料品质合格率不达标。
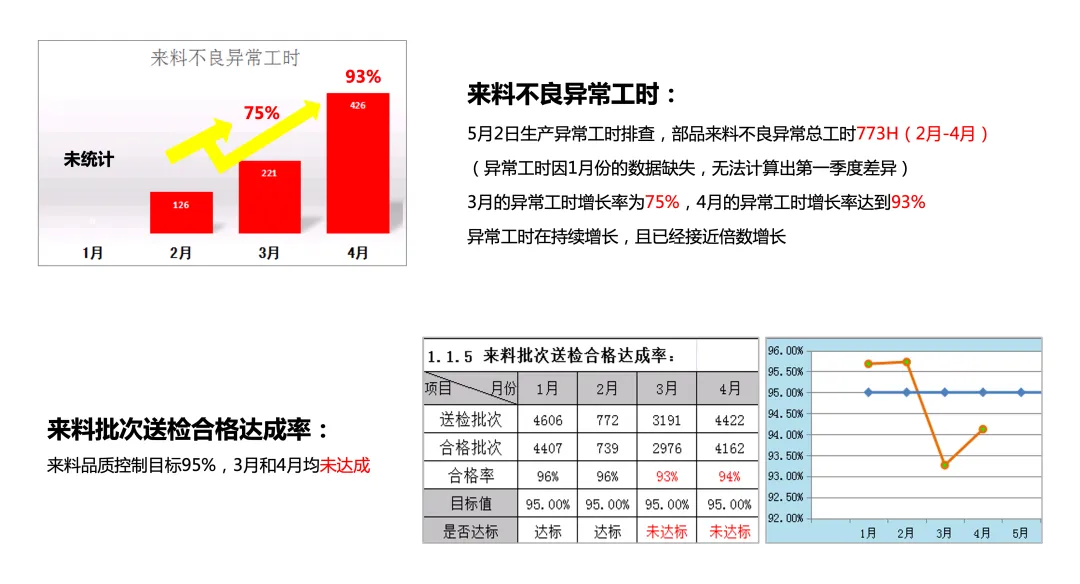
来料品质不合格,将导致制程或最终产品的不合格,造成巨大的损失。可见,A企业对供应商的管理并不够完善。为此,我们与相关部门共同梳理供应商名单,并在1~4月正常交货的供应商中,筛选出部品来料不良前九位,对其状况进行分类汇总。
目前A企业现流机型大部份为试产机种,试产后将逐步移管到公司当地生产,物料在异地受检时变更较快,如仅抓取某一部品改善,将不能有效达成提高来料品质良率。为此,经项目小组讨论后,先行由来料品质不良造成的影响最大的供应商A(4月份送检99批,不良批30批,来料不良率30.3%)进行品质提升,综合1~4月提取的前三项不良现象(脏污、批锋、刮伤)作为改善的切入点,将品质控制点向前推进至供应商。

供应商A前三项不良现象
项目小组分别从脏污、批锋、刮伤三种不良现象进行深入分析,经过一场头脑风暴,找到了现象形成的原因。
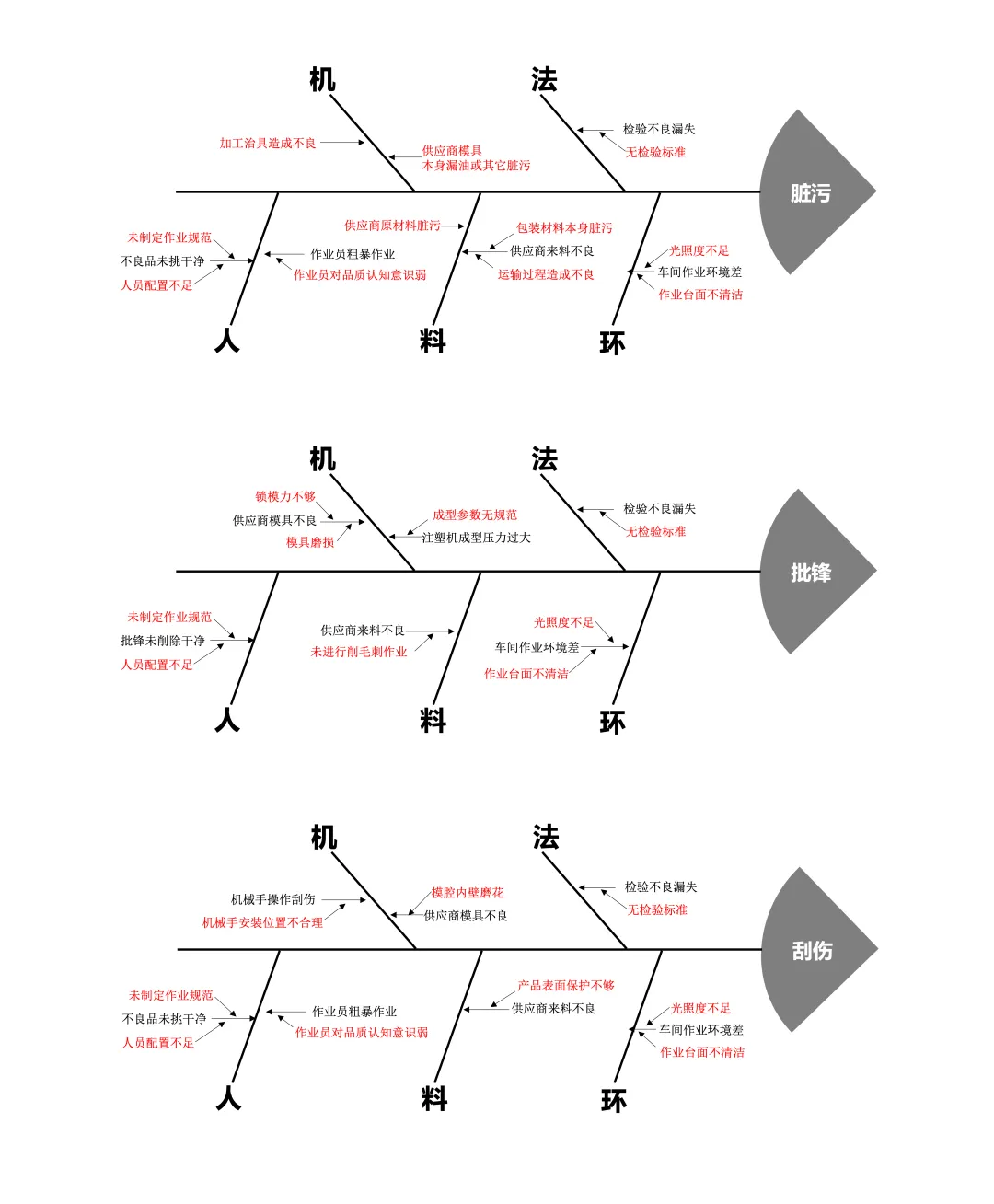
从 “人机料法环” 五个维度进行分析,如上鱼骨图,甄别出三种不良现象总共存在17个末端因素,其中有12个为不同项,有5个为共通项。项目小组根据这些未端因素,回到企业现场进行验证,经验证发现17个末端因素中,存在11个因素为要因,余下的6个并非导致不良现象的原因。
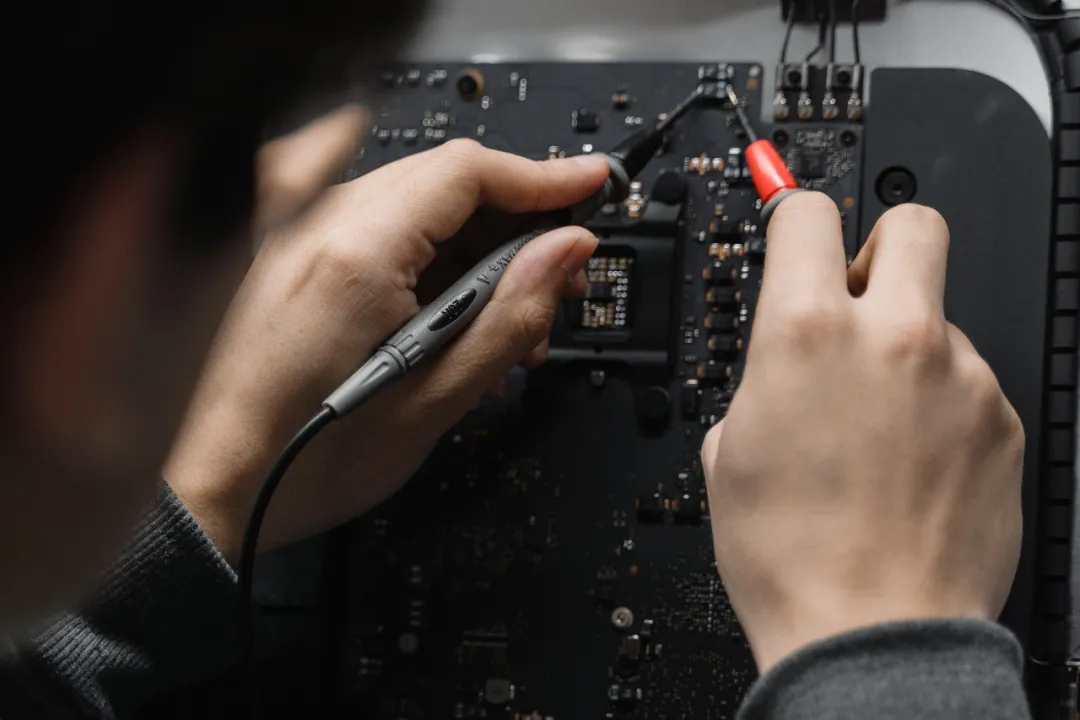
针对11项末端真因,项目小组明确改善措施并制订了子目标。
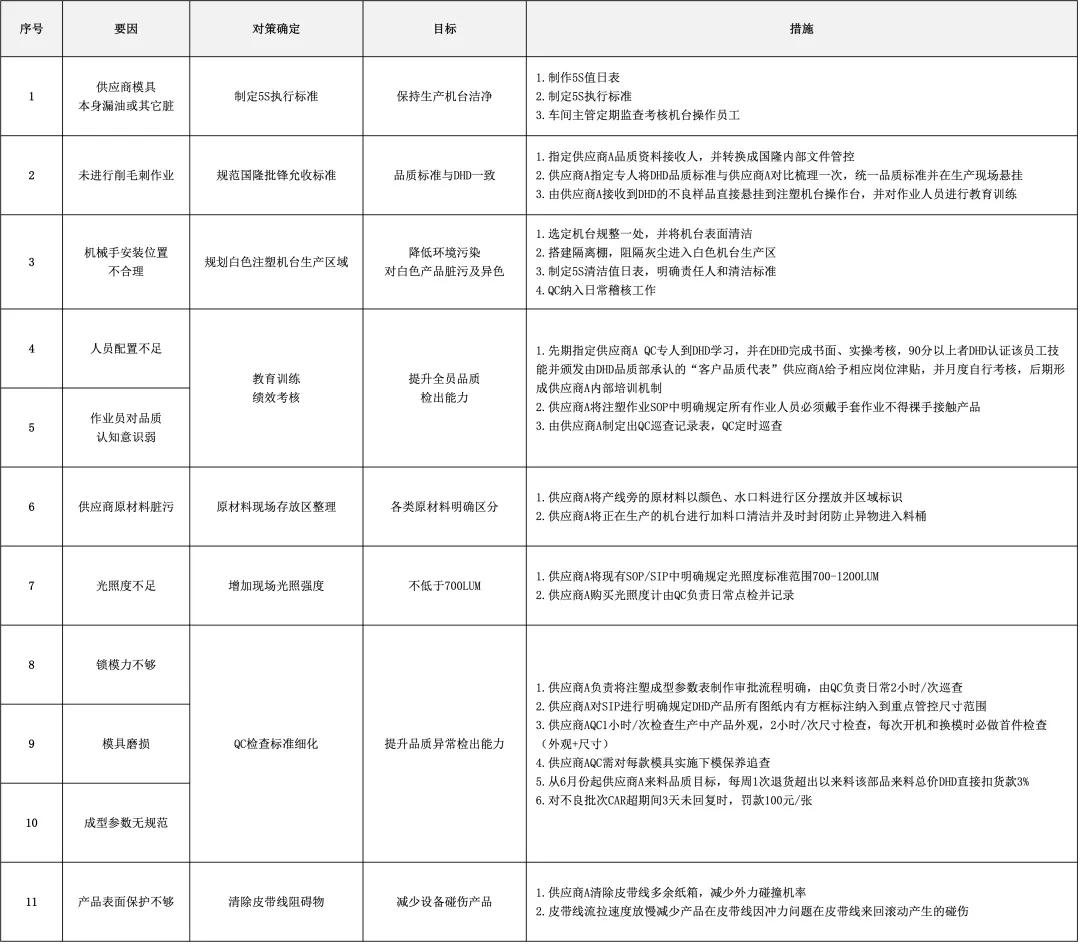
针对末端真因制定目标与措施
在此,我们将针对 “供应商来料品质参差不齐” 的问题,讨论最重要的三项举措。
1. 成型检验指导书
A企业对供应商A的检验环境要求和检验手法没有作出详细的说明,而针对检验员的质量管控要求,虽然有开展不少的培训教育,但却缺乏了相关的依据和标准。
为此,要求供应商与A企业的检验要求统一,将检验要求标注在成型检验指导书上,所有新进员工可按此文件进行培训。
坚持检验环境、手法标准化,消除因检验环境和手法不一致导致的不良流出,提升员工品质意识。
2. 对供应商A的首检与样品管理
首检与A企业提供的不良样品和不良限度样品产线无区分管理,导致样品经常丢失。且在混放后,管理者对首件检查不能快速识别。
为明确不良样品签样标准,我们协助统一供应商A与A企业部品允收标准,由供应商A品质直接对口A企业品质接收品质签样。并提升现场目视化管理程度,在现场将物品放置盒隔开区分 “样品盒” 与 “首件盒”。
3. 供应商A的现场目视化管理
供应商A的检验室内,缺乏现场揭示的相关检验标准及品质管控要求,现场目视化管理程度不足。
经过调整,我们将品质检验标准、品质管控指导书、不良履历、6S管理要求等揭示在现场,作为看板目视化管理。6S管理程度逐渐提高,消除大量的因作业环境杂乱而导致的不良产生和不良流出,同时也提升了现场管理水平。
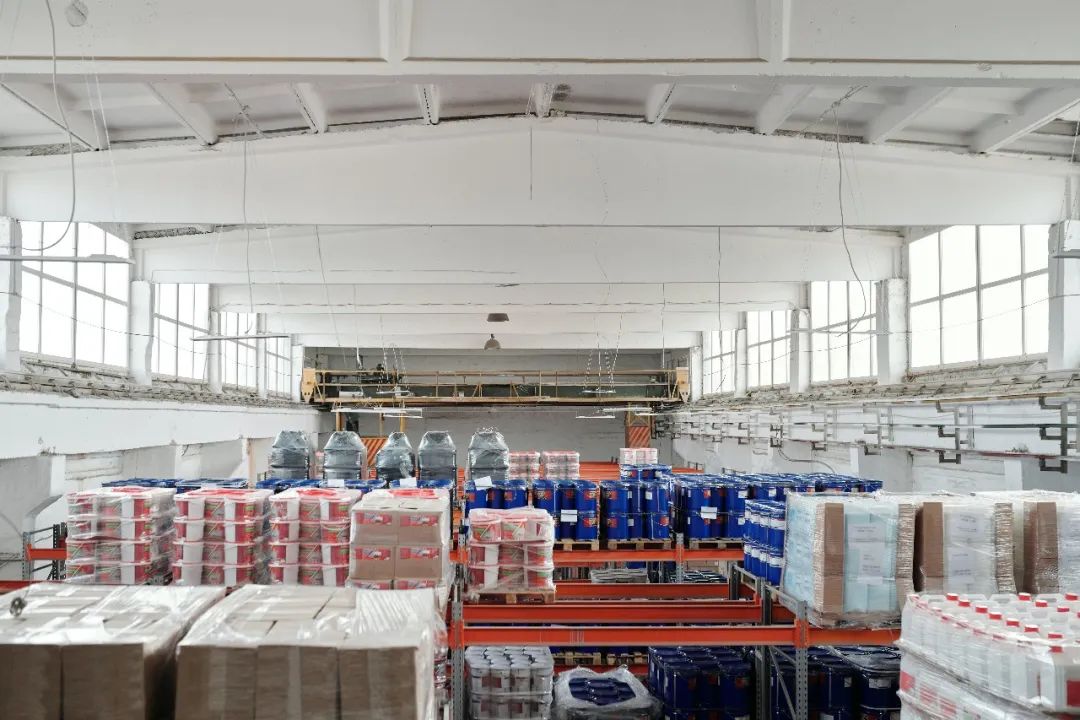
一个月后,来料品质得到了显著的改善。为了确保改善成果的持久性,并防止以上问题的再次出现,我们对改善成果做出了如下标准化管理:
1. 质量数据统计改善
之前所有来料有区分专人进行检验,但未将检验情报及时与供应商通报,不利于对供应商质量管理指明改善方向,质量数据追溯性不足。建立工作微信群,进行来料检验情报日报告、周总结报告,让供应商易于找出质量问题的改善侧重点实施针对性管控提升内部不良拦截及改善。
2. 质量允收标准统一
之前供应商内部的品质标准接收窗口不固定,导致与A企业来料质量允收标准不一致,如开供应商会议后 由A企业品质部IQC重新输送全新的质量允收标准,并规定后续供应商的所有品质标准输送均由IQC负责输送。
3. 供应商监查管理
依据专案活动过程,梳理5月份来料品质数据,提练出10位主体供应商,导入过程辅导,制定供应商整改过程中阶段品质目标,全面提升整体来料受检良率。
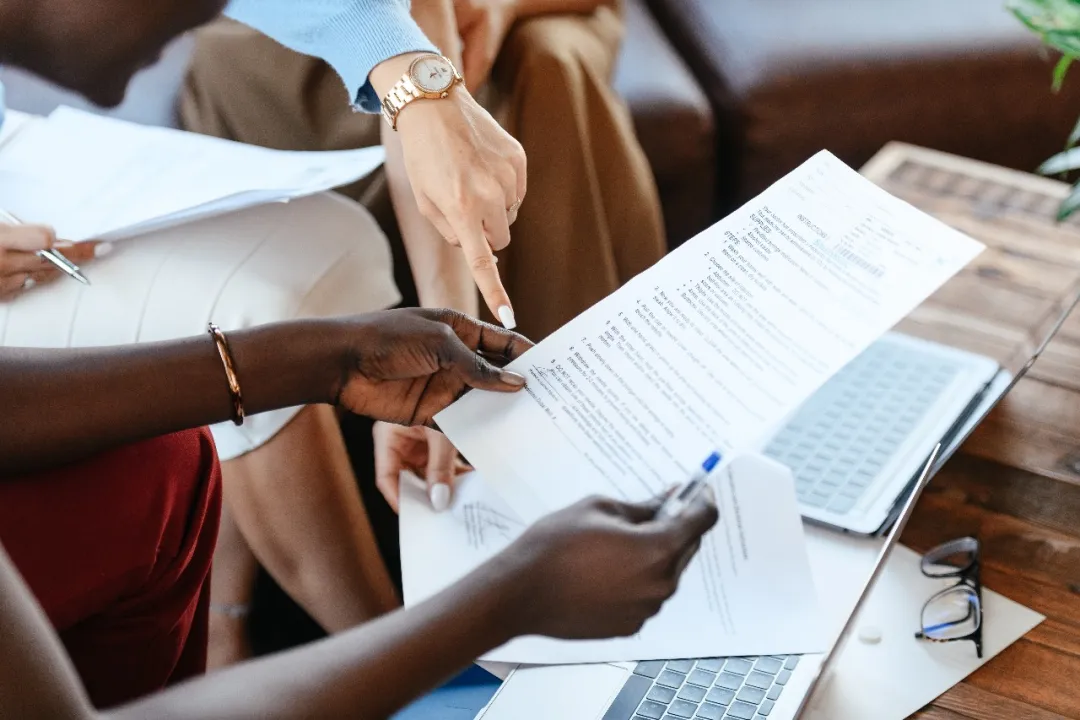
一个月内,我们帮助A企业改善了来料品质——原本30.3%的来料不合格率降低到12%,不仅达成了目标,而且将效果维持在6%。
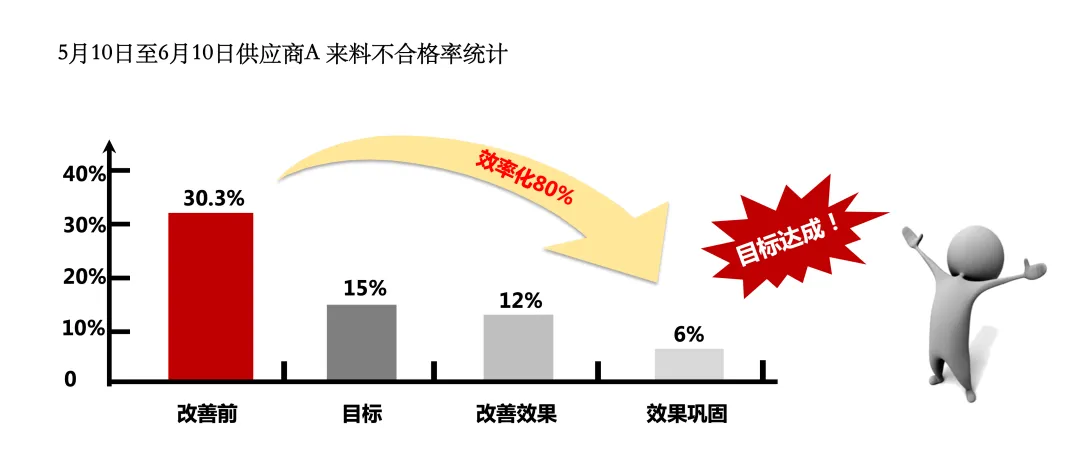
1 | 异常工时降比幅度92% 4月份异常工时426H 5月份异常工时77H |
2 | 异常工时费降比幅度82% 4月份异常工时费6390元 5月份异常工时费1155元 |
3 | 来料合格率提升4% 4月份来料合率94% 5月份来料合格率98% |
4 | 平均来料上线异常件数降比幅度86% 4月平均来料上线异常件数7件 5月份异常件数1件 |
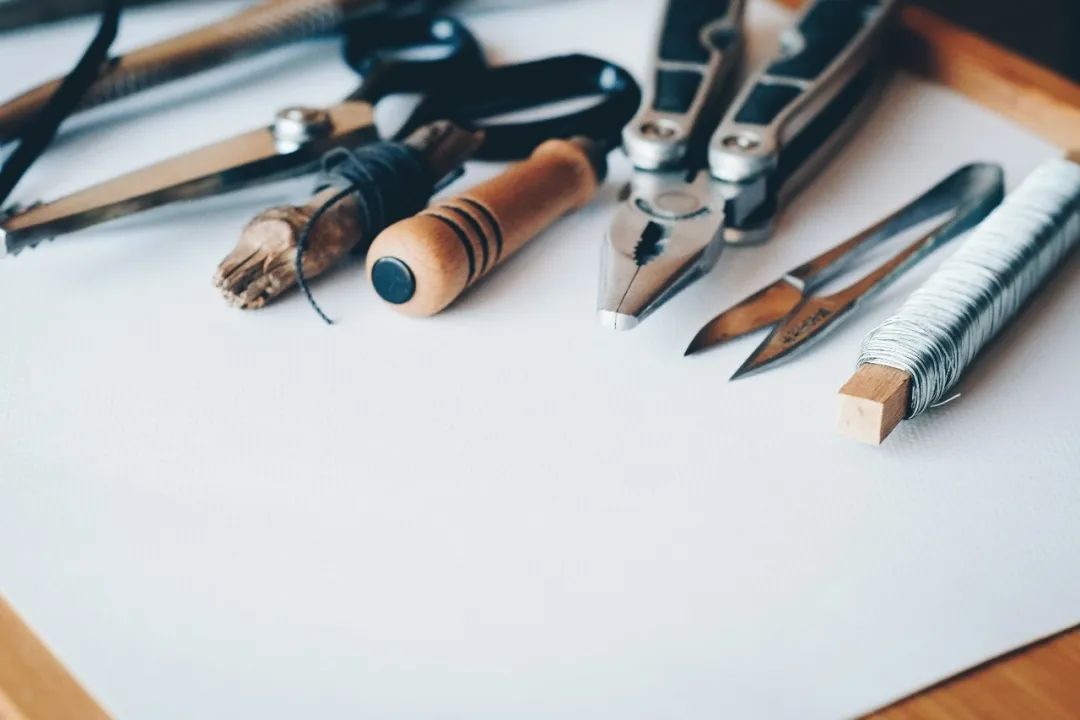
结语
在质量体系健全的公司,质量是 “防” 出来,而不是 “检” 出来的。品质管理是贯穿公司内部、外部的全流程行为。
而现实却是——大多数中小型企业的品质管控部门只充当判官,而没有从体系、标准上去思考并解决问题。
真正减少生产异常、提升品质,并非一个劲在技术上琢磨就行,更多的是对来料标准、检控要求的严格执行、实时跟踪,最终在反馈中不断检讨与改进。
企业内的管理工具和方法不缺乏
但需要系统化并一脉相承